Our Client
Our client, a large OEM parts supplier for a major Japanese car manufacturer, manufactures interior door panels, producing 1,400 parts daily across two shifts. These panels can have up to 95 small features each, including screws, clips, welds, felt strips, SK clips, and switches. Using 3D inspection software we can quickly check through all 95 features.
The manual small part inspection process used to be completed by four operators. Two operators focused on the B-side of the panel where all the fittings are installed
(the side that is not visible to vehicle occupants), and two focused on the A-side of the panel. The B side inspection involved checking for the presence and correct fitments of screws, clips and the other 95-plus features.
Our client required an automated camera inspection system that can perform 100% inline quality control of these features with a 30 second cycle time. Unblink3D solution helped take their manufacturing quality control automation to the next level.
The Challenge
The inspection process for the B-side of the panel, which is the more complex element of the process, needed to be completed in 30 seconds. Using a manual inspection process, the factory noted that a number of incorrectly assembled parts were reaching the customer.
This situation was a major risk for the firm because supplying incorrectly assembled products impacts the customer downstream process could result in termination of the contract. Developing a solution that eliminated human error and downstream defects was a priority.
The Solution – 3D Inspection Software
Unblink3D software solution includes inspection robot motion, product clamping, scanning, data processing and uploading that forms the entire inspection machine. The client was also keen to reduce the cycle timeTo achieve this goal, one Fanuc inspection robot per cell and two line profile 3D scanners were installed working in tandem. Under the control of Unblink3D software, this system provides the necessary field of view to cover a large part in a single pass of the inspection robot arm.
When each part is ready for inspection, the operator loads the door. The B-side of the panel is then scanned by a robotic vision inspection system, and the data is sent to our 3D processing software ScanXtream for point cloud analysis. Each of the features is extracted and compared to the design specifications.
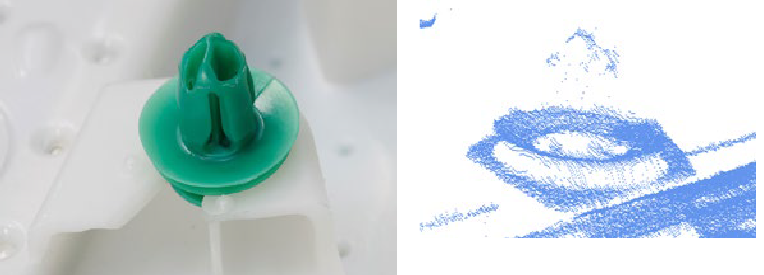
Dog House Clip and Dog House Point Cloud
The results of the analysis are sent to the Unblink3D real-time manufacturing data intelligence software SPCWorks database and the client’s process control software system. While this process takes place, operators check the A-side. If any faults are identified, the part is then sent to the repair station. Parts that pass the inspection process are then dispatched to the shipping racks.
The Results
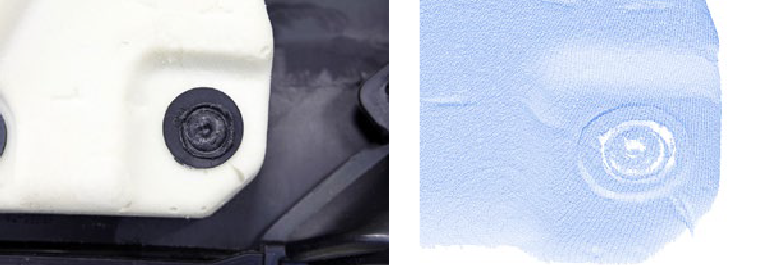
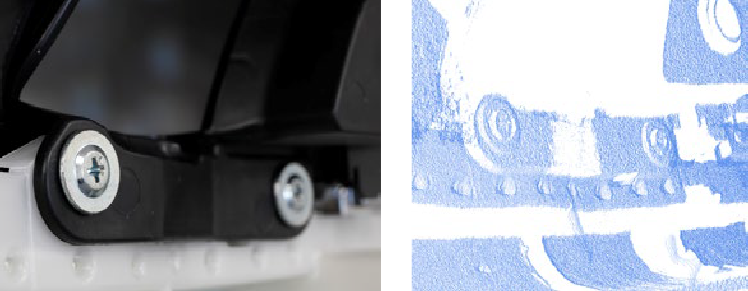
The benefits to our client have been three-fold. First, we have reduced the processing time from 36 seconds to 30 seconds, ensuring that 700 parts are completed every shift and allowing our client to meet its production targets. Second, operating costs have been reduced because the process now requires only two operators rather than four. Finally and most importantly, the overall number of defects has been reduced. This benefit was achieved both within the production line as faults are identified and rectified as part of a process of continuous improvement. Our 3D inspection software identifies common faults so that improvements can be made to the manufacturing process.