Our Client
Our client manages a factory that produces high-precision CNC-machined parts. CNC manufacturing converts computer-aided design (CAD) files into coordinates that control the movement of the cutter machine.
While this process is highly accurate and enables parts to be produced quickly and accurately, CNC cutting sometimes leaves burring along the edges, which may be sharp (a safety risk for workers handling
the parts) and leave accurately cut components slightly outside the specifications. This issue is key for manufacturing parts that require smooth contact surfaces. The burr may also come loose and cause hang-ups or equipment damage in the downstream process. 3D scanning quality control deburring is, therefore, an important finishing process for ensuring that components are not left with rough or sharp edges.
The Challenge
Because the firm manufactures hundreds of unique parts of different shapes and sizes, the location of any burring is nearly always different and not always easily identifiable using human visual inspection. However, identification is essential for ensuring that surfaces are safe to handle and manufactured to acceptable tolerances.
Because burrs are irregular, they show dramatic fluctuations in curvature in small segment boundaries of each CNC cut edge. Where a segment is smooth, it is because of a succession of low curvature points along the boundary, suggesting that deburring is not required.
Unblink3D software solution combined with a 3D vision sensor, this solution can be mounted on both fixed gantries and robotic arms as required, based on the size of the part and the coverage required.
As each part is scanned, a 3D point cloud image is produced that is then sent to our 3D processing software ScanXtream for comparison with the original CAD drawing. This process flags any deviation from the pre-defined tolerance as a potential burr and notifies quality assurance staff immediately so that remedial action can be taken.
The Results
Under the control of Unblink3D software, this solution enables 100% 3D scanning quality control inspection of all parts, which means that Unblink3D real-time data intelligence software SPCWorks, integrated into the process, can report on production trends, variances, and stability. This tool allows our client to monitor both production quality and the level of wear on any CNC tool (burring may be the result of a tool that needs to be replaced). The overall results of our work with this client ensure improvements in the downstream manufacturing processes because all inconsistencies are addressed as part of the manufacturing process.
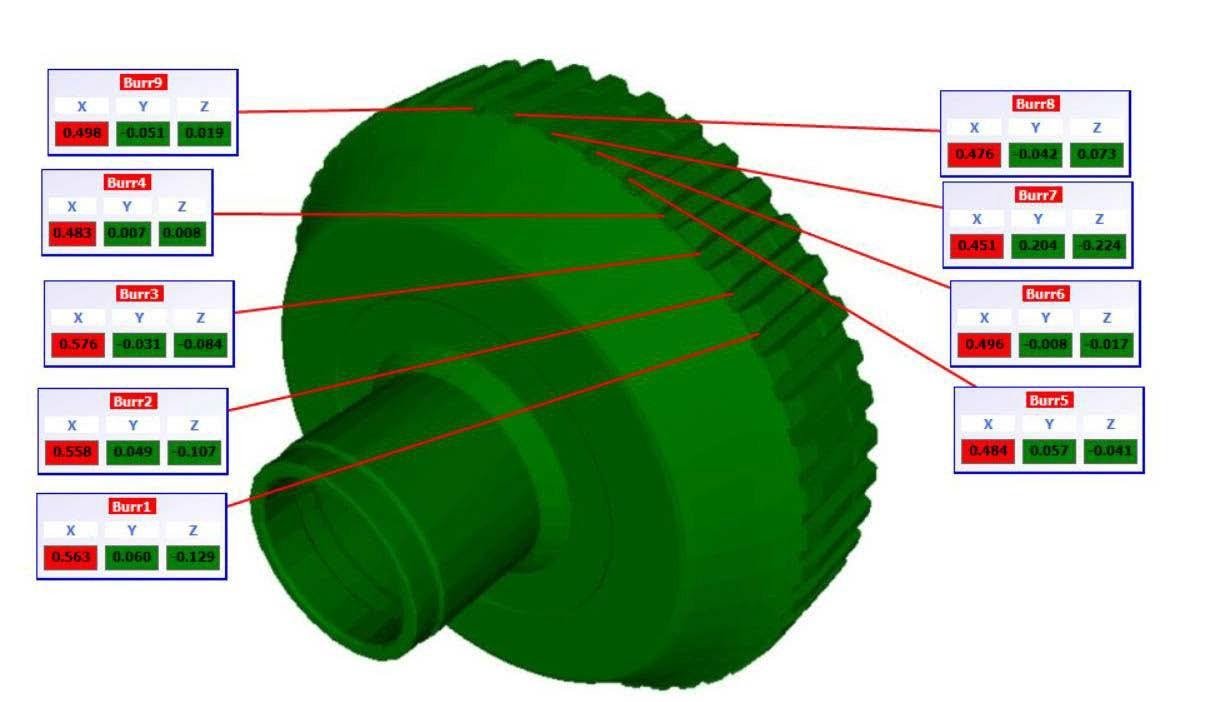