Background
To meet rising electricity demands of growing cities, existing nuclear power plants must undergo refurbishments to increase the power generation output safely and to cope with the growing power consumptions in the next half-century. Existing nuclear power plants in North America have been in continuous operations for more than two decades and will require extensive upgrades to their reactor cores as part of the refurbishment process. Unblink3D 3D processing software ScanXtream to handle 3D scanning concentricity inspection is used to verify the quality of the components used in this project.
At the heart of the refurbishment process is the re-tubing of the reactor core, which consists of 380– 480 fuels channels housed in individual pressure tubes. The pressure tube resides within another cylindrical housing made of zirconium alloy that acts as the secondary pressure containment safety device in the event of a main pressure tube rupture or failure. This housing is thermally separated from the pressure tube by garter springs and an annulus gas system using carbon dioxide. All of these components must be replaced as part of the re-tubing and refurbishment process. To reliably provide power generation for the next half-century, the pressure tube housing must be manufactured under the highest quality tolerance to ensure the reactor’s safety and operational longevity. Unblink3D software expertise in monitoring and analyzing manufacturing dimensional data played a key role in the inspection process to help aid in the quality control of this pressure housing.
Challenges
The company awarded the refurbishment contract must manufacture several hundred of this highly specialized cylindrical housing. Each housing is six meters in length with an outside diameter of 132 mm and weighs about 25 kg. They must be designed to withstand a pressure of 25 MPa and a water temperature of up to 208 degrees Celsius. The housing is exposed to such conditions throughout the operational life of the nuclear reactor and must remain structurally intact for the next three decades. To verify the manufacturing process capability and to guarantee the product quality, more than 800 inspection points need to be performed on each cylindrical housing unit to detect microscopic flaws or deviations from tolerance.
Some of the critical features inspected include the following:
•Inner and outer diameter
•Housing wall thickness at various sections
•Concentricity
•Ovality
•Parallelism
This inspection process generates a large amount of dimensional data that must be correlated with CMM measurements and stored for traceability and quality reporting purposes.
Our Solution – 3D Scanning Concentricity Inspection
Due to the size and the unique structure of the cylindrical housing, Unblink3D real-time data intelligence software SPCWorks for statistical process control allowing for the measurement and data capture of all the key inspection points for each of the cylindrical housing units manufactured.
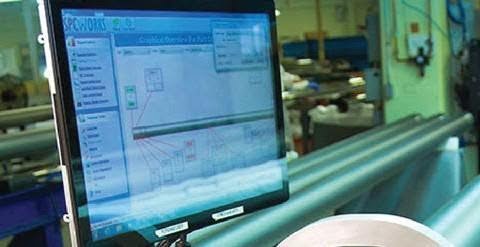
The Results
After the deployment of the 3D scanning concentricity inspection software solution, the manufacturer used the dimensional data captured by the 3D laser cameras and reports generated by SPCWorks to verify the process capability and stability of the production process. As a result, the manufacturer is able to deliver the first shipment of the cylindrical housing units to the customer ahead of schedule while meeting and exceeding all the stringent quality control criteria.